More resilience in the supply chain
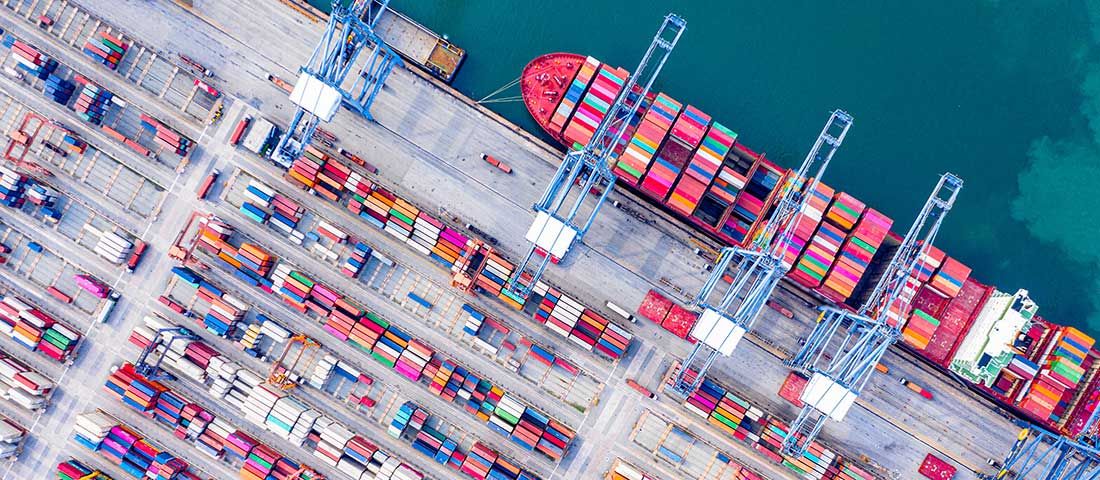
How to successfully switch to resilient production planning and logistics
Stuttgart, Germany, July 2021. Restrictions during the Corona pandemic, the blockade of the Suez Canal by a container ship and the resulting supply bottlenecks in the chip industry, among others, have shown how vulnerable the global network economy is. Balancing fluctuating sales figures, production capacities and different logistics requirements is becoming increasingly difficult and at the same time more important. One essential element in overcoming these challenges is consistent digitization. This can be achieved with the support of four technologies for a resilient supply chain: cloud, AI and machine learning, digital twins and the CORE planning model. What is important to keep in mind?
For decades, supply chains have been more simply organized, tightly timed, and requirements highly reliable. Accordingly, planning was - and often enough still is - deterministic, based on fixed production schedules and material requirements. With this approach, however, limited or inaccurate information can cause massive disruptions. Some companies rely on very large buffers as a countermeasure, which is often associated with high inventory costs. A model that overcomes these weaknesses, on the other hand, actively monitors buffers and works with holistic, order-based planning processes.
Towards a resilient supply chain in four steps:
A resilient supply chain adapts to disruptions and changing circumstances without costly interruptions and outages. To achieve this, companies need processes that scale quickly and easily. Data analysis and planning adjustments must be made in real time, and different levels of planning (e.g., tactical, strategic, and operational) must be able to be integrated into a cohesive whole with a high degree of visibility. These four technologies are particularly important:
-
Cloud: Running IT on servers in your own data center (on-premises) can lead to data silos, faulty IT integration and scalability issues in an increasingly connected supply chain. With cloud technology, these problems are essentially a thing of the past. The cloud provides the responsive digital foundation needed for integrated planning - at lower internal IT costs. This is due to the operating model, in which billing is based only on actual consumption, usually monthly. The technology itself for example, makes rolling out new features to assets up to 200 times faster than in non-cloud environments.
-
AI and machine learning (ML): speed plays a big role in resilience. AI and ML analytics tools can help capture and analyze data much faster and much more comprehensively than before. Based on this, production and logistics planners can improve forecasts, optimize networks, and dynamically adjust plans.
-
CORE planning model: As outlined by Gartner, the CORE (Configure, Optimize, Respond, Execute) model helps connect different supply chain planning dimensions into an integrated whole by breaking down silos between business units that are separate today. It helps to combine planning, optimization, operational control and execution into an integrated planning funnel in consideration, taking a holistic view of the entire supply chain. Again, the technological foundation is cloud or cloud-based platform technology, which enables supply chain planning solutions to be combined and linked.
-
Digital twins: representations of the data in a digital twin enable scenarios to be created in real time. This allows decisions to be made based on sound information, which in turn leads to increased resilience. Many companies already use digital twins to model production or other processes. But the linchpin is to combine them all into a single model that encompasses the entire supply chain. In this way, synchronicity is created within the larger CORE model.
Meeting the challenges of a supply chain that is at risk in many ways requires a "Logistics 4.0" approach that looks at the entire supply chain. The goal is to establish the highest possible level of resilience despite an increasingly complex supply chain management and network.
"Supply chain and logistics 4.0 systems from flexis increase operational efficiency by making processes more responsive and flexible, and by enabling networked and collaborative planning and execution monitoring. Our customers benefit from accelerated business growth - primarily through improved forecast accuracy by up to 20 percent, reduction of short-term planning changes by about 25 percent, and reduced inventory levels by about 20 percent," comments Robert Recknagel, Vice President Manufacturing and Logistics at Stuttgart- based flexis AG.
Further information is available in this Whitepaper
Guide to Supply Chain Resilience and the New Normal
about flexis
flexis AG specializes in flexible information systems for supply chain management. With more than 20 years of experience in providing standardized software modules, the company offers customized solutions based on secure and proven modules. With seven locations worldwide, flexis AG is globally networked and acts as a close partner and support service provider for over 1,000 satisfied users, even after successful implementation. Our focus is always on the customer's continuous improvement process.
flexis’ Supply Chain Solutions are based on the flexis HYBRID Architecture. Our modular, customizable solution modules, unique software technology, and numerous other services power intelligent ways to optimize your processes -for a wide range of industries with national or international networks. Our primary goal is to create real added value together with our customers. flexis maintains long-term and trusting business relationships with customers and partners and contributes to their success with a deep understanding for the process world across multiple industries.
contact:
Ute Schmidt
Head of Marketing
Tel: +49 711 782380-153
ute.schmidt@flexis.de
flexis AG
Schockenriedstr. 46
D-70565 Stuttgart
www.flexis.com