PACCAR's Journey with flexis
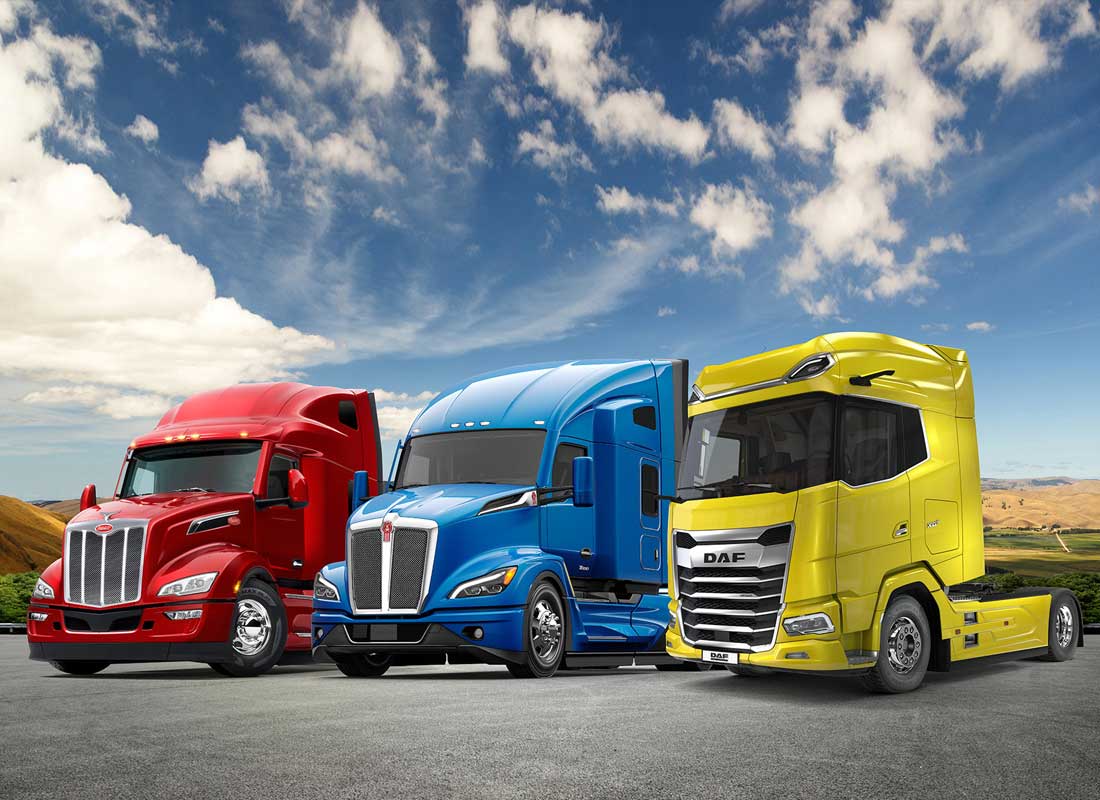
Status
PACCAR, a global leader headquartered in the US, specializes in the design and manufacturing of large commercial trucks. With renowned brands such as Kenworth, Peterbilt, DAF, and Leyland under its umbrella, PACCAR operates manufacturing facilities across the US, Canada, Mexico, Australia, the Netherlands, and the UK. The company’s extensive portfolio demands a robust production scheduling system to handle its diverse and complex operations.
Challenges
In the initial stages, PACCAR sought a solution to accommodate the highly customized nature of its truck production. Each assembly line dealt with a vast array of truck configurations, necessitating a production scheduling tool that could manage the following complexities:
- Complex Order Configurations: In the Engineer-to-Order environment, each order is unique in content and complexity, creating a very dynamic and changing production environment.
- Diverse Plant Requirements: Each manufacturing plant varied in size and the types of trucks produced, requiring a flexible scheduling solution.
- Multiple Attributes and Constraints: The scheduling tool needed to consider numerous attributes and constraints to optimize the assembly line flow and productivity.
- Complex Rules and Flexibility: The system had to handle intricate production rules, adapt to new or modified constraints, and operate with high efficiency.
- Integration Needs: Seamless integration with PACCAR’s existing mainframe system for data import and export was crucial.
Solution
After a thorough review of various software solutions by PACCAR’s ITD teams in the US and Europe, flexis was chosen for its ability to meet these stringent requirements. A workshop involving flexis and multiple PACCAR IT and business personnel confirmed that the APS application was the ideal solution.
- Advanced Planning & Scheduling (APS): The APS application by flexis was implemented to address PACCAR’s production scheduling needs. This tool offered:
- The ability to consider multiple attributes and constraints in creating production schedules.
- Flexibility in adding or updating attributes and constraints.
- Configuration for different plants, various products, each with unique requirements.
- Handling of specific scenarios, such as multi-color paint jobs requiring additional time in certain areas.
- Monitoring of truck production to ensure adherence to constraints and optimize workflow.
Result
The implementation of the flexis APS application has delivered significant benefits to PACCAR, enhancing their production scheduling capabilities and overall operational efficiency.
- Optimized Scheduling: The ability to consider multiple attributes and constraints has streamlined the creation of balanced production schedules.
- Flexibility and Customization: The system’s flexibility allows for easy updates tailored to each plant’s needs.
- Enhanced Productivity: Improved assembly line flow and labor usage have resulted in optimized productivity.
- Comprehensive Monitoring: The tool enables PACCAR to quickly identify and address over or under constraints, ensuring smooth and balanced production operations.
Long-Term Partnership
PACCAR has been utilizing the flexis APS application since 2005, with the first North American implementation in 2007. Over nearly two decades, PACCAR has maintained a strong relationship with flexis, benefiting from their expertise, creativity, and exceptional customer support. This long-term collaboration has been marked by continuous improvement and mutual success, with PACCAR consistently achieving its production goals thanks to the robust capabilities of the flexis APS application.